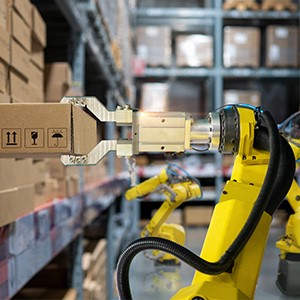
As a key issue for forward-looking companies, smart warehousing represents the future. Thanks to an automated system that interacts with other elements of the logistics warehouse, the total optimisation of the supply chain can increase a company’s productivity. To help you understand all these innovations, we have put together a detailed article on logistics warehouse automation and its future in the industry.
What Is a Smart Warehouse?
Today, the number of smart warehouses is constantly growing in order to respond to developments in the logistics sector and the needs of its stakeholders. Automation offers numerous benefits for professionals. There are various solutions out there to help apply these innovations to the reality on the ground and the specific situation in each company.
The Benefits of a Logistics Warehouse With an Automated System
The world of business is changing every day and demands ever-increasing productivity, especially when it comes to order picking and product delivery. Automating logistics warehouses allows companies to keep up with this pace and to meet the expectations of customers.
Within an automated warehouse, the initial organisation of the company is used as a foundation that dovetails with advanced technology for optimisation in both the short and long term. By means of an adjustable and scalable organisation, a logistics warehouse with an automated system therefore aims to increase optimisation and productivity.
It adapts in real time to multiple factors such as inventory management and unexpected issues linked to the receiving, shipping or traceability of products. Thanks to the coordination of these different factors and the automated system, a logistics warehouse offers the possibility of a stable, flexible and efficient organisation in terms of productivity.
From goods receiving to order picking or product storage, each automated system is integrated into the supply chain. The automated warehouse coordinates the supply chain for improved optimisation of the entire production chain. Logistics warehouse automation also eliminates repetitive tasks, allowing employees to focus on operations that add value with regard to productivity.
The Main Solutions Used in a Logistics Warehouse With an Automated System
Logistics warehouses make use of automation, notably in operations, thanks to handling equipment or robots utilised in combination with advanced technologies. Logistics warehouses with an automated system are based on three major technologies:
- WMS (Warehouse Management Systems), or logistics warehouse management software;
- RFID, or radio-frequency identification systems;
- Disruptive technologies.
Among the advanced technologies used to optimise order picking within the supply chain, the most common automation solutions are:
- Artificial intelligence;
- Big data;
- Machine learning;
- Augmented reality;
- Connected sensors.
An Automated System That Dovetails With the Company’s Ecosystem
The WMS is integrated taking into account the pre-existing organisation in order to offer lasting solutions and appropriate, adaptable implementation. The optimised warehouse – thanks to an automated and interconnected system – is therefore integrated into the company’s ecosystem, and in particular the supply chain. In addition to effective storage control and efficient operations planning, it also provides better visibility to customers.
Added to this is an optimised response to external factors, such as unforeseen issues linked to storage or delivery. A logistics warehouse with an automated system thus boosts productivity by offering quick and efficient solutions.
It not only adapts to the company’s supply chain but also dovetails with all external systems, such as the real-time visibility over stock at each point of sale. Automating the logistics warehouse thus provides a comprehensive overview of all elements connected to the logistics flow in order to anticipate unexpected issues and deal with them at a given moment (T) with maximum responsiveness. This fundamental element allows the company to be highly adaptable, significantly improving the execution of operations and the company’s productivity.
How to Make the Switch Too Smart Warehousing
There are several optimisation options available to professionals who wish to begin or continue automating their warehouse; they can therefore select the solution that best suits their needs and their constraints.
Practical Solutions for Efficient Automation
In a logistics warehouse with an automated system, stacker cranes or drones replace forklifts. This means that manual operations are no longer carried out by employees, but rather by an optimised system supported by robotics. There are three solutions that can be employed to streamline all operations carried out in a logistics warehouse:
- Order picking: robotic arms, high-performance picking stations and voice picking are automatic solutions that optimise order picking.
- Warehousing automation: stacker cranes, wire-guided vehicles or pallet shuttles streamline the storage and retrieval of goods during shelving.
- Transport optimisation: drones or autonomous robots and cobots reduce a product’s travel time in the different areas of the warehouse.
Software for an Efficient Logistics Warehouse
Logistics software is installed in the company’s ERP system to monitor all warehouse inventory and ensure the permanent traceability of each product. Three automation solutions can help optimise your logistics warehouse along the entire supply chain:
- The WMS, or Warehouse Management System software package, synchronises and coordinates all operations, from order entry and storage control through to picking and product output.
- The WCS, or Warehouse Control System, allows you to manage handling equipment activity in real time.
- The MES, or Manufacturing Execution System, dovetails with the supply chain for improved overall organisation, from task allocation to quality control.
Advanced Technology for a Smart Warehouse
Several solutions can improve your smart warehouse. Below are the three main ones:
- RFID tags;
- Big data;
- Artificial intelligence of things.
Radio-frequency identification (RFID) systems allow you to manage the location of inventory without using individual tags. In this sense, RFID tags are the future of traditional bar codes. They work using radio waves, indicating the location of all inventory. Although they are not mandatory in a smart warehouse, they save valuable time because they eliminate the work of having to read individual tags.
Big data enhances the supply chain by gathering data and analysing all operations. By combining these two elements, big data identifies and studies each operation carried out within the warehouse and then suggests improvements. Big data thus represents the future of supply chain optimisation, because it ensures ever-increasing productivity and adapts to changes in the world of business.
The artificial intelligence of things – or AloT – combines two technologies: the IoT and artificial intelligence. It streamlines how objects interact with each other and simplifies or even eliminates the need for human intervention. The artificial intelligence of things therefore gathers data and analyses all operations to make autonomous warehouses (also known as dark warehouses) possible. These dark warehouses optimise resources and increase productivity by cutting out unnecessary tasks. They are now establishing themselves as the standard for the warehouse of tomorrow.
Why Choose a WMS?
The WMS is an essential element in automating a logistics warehouse. It allows professionals to effectively oversee and manage the running of operations to ensure that the company’s performance is constantly improving.
Using a WMS for the Logistics Warehouse of Tomorrow
Thanks to cutting-edge technology, the WMS and the physical world can constantly interact, thus improving the company’s productivity. This constant dialogue allows the WMS to control the machines and allows the machines to pass information to the WMS that can be reused in order to optimise various operations.
The Advantages of an Automated, WMS-Linked System
The interconnection between the WMS and the physical world delivers increased productivity and a higher quality of service.
This permanent communication streamlines the entire supply chain, increasing responsiveness, improving the picking of each order, and distributing tasks more intelligently. Within a logistics warehouse, all operations are assigned at the right time to reduce unnecessary travel and actions.
This automated system and the solutions it offers allow precise control and traceability of the entire supply chain, from picking to loading, including the putting together and shipping of packages.
The WMS: A Work Solution for the Warehouse of Tomorrow
The WMS is the future of the warehouse management system and the ‘brain’ of tomorrow’s warehouse. It coordinates all operations within the warehouse, from order picking to shipping. Above all, it allows you to manage three future warehouse trends:
- Dark warehouses;
- Wave picking;
- Cross-docking.
In addition to enhancing control, streamlining travel and increasing performance, the WMS is also very flexible. Both sustainable and scalable, it is therefore establishing itself as a solution for the future. Thanks to its adaptability, it is capable of assimilating new technologies and market trends.
Leave a Reply
You must be logged in to post a comment.